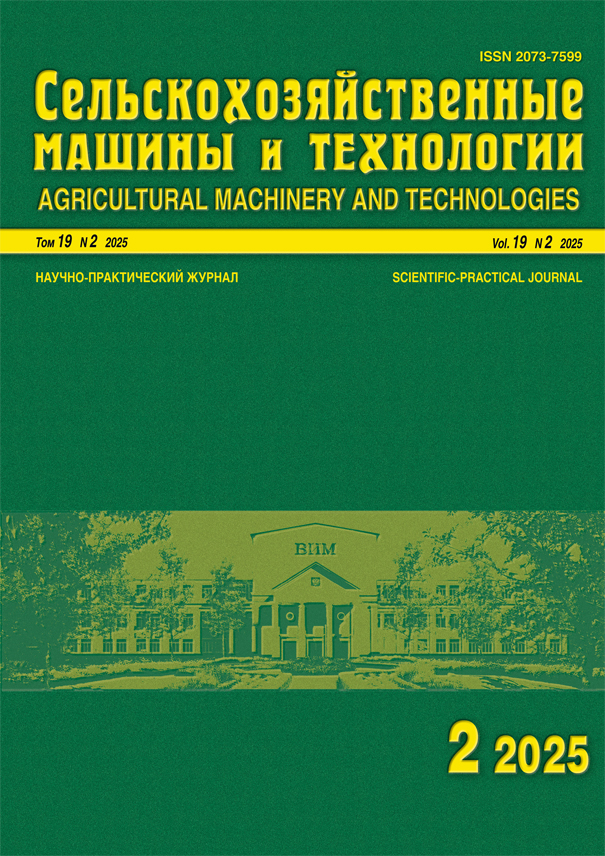
Scientific-theoretical Peer-reviewed Journal «Agricultural Machinery and Technologies» ( «Sel'skokhozyaistvennye mashiny i tekhnologii» )
The journal presents materials about the technologies for various directions developed by domestic and foreign agricultural science: energy saving methods of crops cultivation, rational environmentally-friendly methods of application of fertilizers and plant protection products, low-cost methods of production and preparation of forages, rational use of the electric power, renewable energy resources, biomass fuel processing, deployment of precision agriculture using GLONASS systems, development of technologies of robotics, mechatronics, application of nanotechnologies in agricultural industry.
Innovative scientific component is the contribution of the journal to creation of the domestic energy-resource-saving technologies of agrarian production for the economic, ergonomic, ecological and social safety of the country in the perspective of import substitution in agricultural machinery.
The journal prefers to publish materials about the progressive directions of machine production technologies in crop and livestock production. This fact mainstreams agrarian science for development of agricultural industry on the way of an intensification on the basis of use of the latest scientific and advanced experience achievements.
Current issue
ECOLOGY
Modern production increasingly relies on the implementation of automated control systems to improve the efficiency, precision, and safety of technological processes. In the agricultural sector, complex technologies involve the processing or disposal of organic waste through biotransformation or degradation. These processes occur in multiple phases, each requiring specific operating conditions. To enhance overall effectiveness, there is a need for an automated system capable of monitoring the biothermal reaction process and managing the operational modes of a biofermenter in accordance with the current phase of organic waste processing. (Research purpose) The aim of this research is to develop an automated control system for a drum-type biofermenter. (Materials and methods) The study was conducted using an experimental drum-type biofermenter operating under conditions of aeration of the processed organic matter. The automated control system is built on a three-level architecture: the upper level consists of a server and an operator’s automated workstation, the middle level includes a programmable logic controller, and the lower level comprises sensors and actuators. Temperature inside the bioreactor is measured using resistance temperature detectors housed in immersion sleeves. Airflow is calculated based on readings from a diff erential pressure sensor. The drum’s rotation speed is monitored using an optical non-contact sensor. (Results and discussion) The proposed control system enables automated monitoring of key processing parameters and supports effective management of the biofermenter’s operating modes. Testing demonstrated the system’s ability to accurately monitor and display the mixture temperature, aeration airfl ow, and drum rotation speed. The system also allows for rapid mode adjustments to operating modes and facilitates the identification of optimal parameters for efficient organic waste processing. (Conclusions) The automated control system for organic waste processing in a drum-type biofermenter ensures continuous monitoring of key parameter. This capability facilitates the identification of optimal operating modes and the development of adjustment algorithms tailored to different types of organic mixtures, ultimately contributing to the production of a high-quality end product.
The technology for cultivating hybrid sunflower seeds is formalized as a biotechnical dynamic system structured around the «operator–machine–environment» triad. The efficiency of this system depends on multiple factors, primarily the qualification level of machine operators, the technical advancement of the machinery, and the conditions of both the production and external environments. (Research purpose) To enhance the efficiency of hybrid sunflower seed production technologies by developing and validating safe scientific and technical solutions. (Materials and methods) The system is characterized as probabilistic, with its state described by a mathematical model. The model’s input variables represent factors exerting positive, neutral, or negative impacts on the system. It is established that achieving optimal system performance requires the rational distribution and effective coordination of energy, material, and information flows across its subsystems. (Results and discussion) The study demonstrates that the research objective is achieved through two core systems engineering tasks: analysis, which involves identifying key parameters of the biotechnical system and environmental variables that exhibit probabilistic-statistical variability; and synthesis, which involves justifying an optimal control scheme for system operation. (Conclusions) The technological reliability of the biotechnical system, as a qualitative metric, reflects its capacity to perform designated functions while accounting for technical and economic indicators, ecological and ergonomic requirements, and time-related factors. Ergonomic requirements related to system design and parameter selection must take into consideration injury-inducing factors that affect the safety of hybrid sunflower seed production technologies. The convergence of pre-injury conditions and hazardous operator actions in time and space leads to injury, the occurrence of which can be mathematically modeled as a function. A comprehensive indicator – the injury risk criterion – is proposed and modeled as a function of harmful factors, including workplace dust concentration, ambient temperature, and the technical condition of the machine-tractor unit. A predictive model has been developed to estimate the number of potential injuries, and corresponding preventive measures have been substantiated. The agrotechnological application of the proposed model enables a 12-15% reduction in injury rates and facilitates the transition to safer cultivation technologies for hybrid sunflower seed production.
DIGITAL TECHNOLOGIES. ARTIFICIAL INTELLIGENCE
The study proposes a novel method for reconstructing missing regions in depth maps, aimed at improving the accuracy of autonomous navigation in agricultural robotic systems. (Research purpose) The primary objective is to develop a method capable of compensating for data loss in depth maps, thereby improving the performance of Simultaneous Localization and Mapping (SLAM) systems. (Materials and methods) The depth map reconstruction method consists of three main stages: computation of the anisotropic gradient; identification of similar blocks based on a novel similarity criterion; and merging of the detected blocks using a neural network architecture composed of an encoder, a fusion layer, and a decoder. The method was tested using the Rosario dataset, which includes scenarios representative of complex agricultural environments. (Results and discussion) The proposed depth map reconstruction method demonstrates a significant improvement in quality metrics. Specifically, Root Mean Square Error (RMSE), Peak Signal-to-Noise Ratio (PSNR), and Structural Similarity Index Measure (SSIM) improved by 20–30 percent compared to the existing techniques. The method preserves the structure and texture features of the reconstructed regions, enabling accurate restoration of large areas with missing pixel data. To evaluate the impact on SLAM performance, the Stereo Multi-State Constraint Kalman Filter (S-MSCKF) algorithm was employed. Quantitative analysis of Absolute Trajectory Error (ATE) and mean RMSE was conducted both before and after applying the depth map reconstruction. The results show a reduction in Absolute Trajectory Error from 0.62 meters to 0.25 meters, and a decrease in Root Mean Square Error from 0.85 meters to 0.39 meters. (Conclusions) The proposed method substantially enhances SLAM system accuracy, particularly in challenging agricultural environments, characterized by uneven terrain, variable lighting conditions, and long-distance navigation. Its robust performance suggests strong potential for large-scale integration into autonomous agricultural machinery, contributing to improved reliability, operational efficiency, and safety in robotic field operations.
The current global economic and environmental context, which is characterized by desertification, land degradation, climate change, and ecosystem disruption, necessitates urgent action in sustainable land use. While pasture-based livestock farming offers numerous advantages, free-range grazing presents several labor-intensive challenges, such as locating and tracking animals, monitoring livestock health, mitigating the risk of loss in wild environments, and regulating grazing pressure on pastures. (Research purpose) To develop a digital pasture infrastructure as a universal, integrated system with autonomous energy and water supply, aimed at automating auxiliary processes in pasture-based livestock farming. (Materials and methods) Various approaches to improving pasture efficiency were reviewed. The analysis revealed that existing technologies typically address isolated aspects, such as water supply, pasture rotation, or livestock monitoring. However, they lack a comprehensive system that integrates the entire pasture infrastructure and the interactions among its components. (Results and discussion) A digital pasture concept based on renewable energy sources is proposed. An integrated infrastructure model for pasture-based and transhumant livestock farming was developed. The system consists of distinct infrastructure modules, including communication, monitoring, water supply, electrification, transportation, a central dispatch unit, and a supplemental feeding unit. Several components were developed and patented, including individual livestock blankets equipped with condition sensors, a monitoring station, a wind power unit, and an atmospheric water extractor. The monitoring station, capable of data collection, control, monitoring, and communication using renewable energy, was field-tested in the Astrakhan Region. The sensor-equipped livestock blankets were tested on a pilot group of calves in the Yaroslavl Region. Field trials of the atmospheric moisture extractor were also conducted. Additional trials are underway in southern regions and the Moscow Region to evaluate the performance of a multi-unit wind energy complex designed for areas with low wind potential. (Conclusions) The modular architecture of the proposed system enables flexible integration of various technologies and functional units, adaptable to the specific needs of local production conditions. The development and implementation of a digital, intelligent infrastructure for pasture-based and transhumant livestock farming, based on resource-efficient, nature-based, and digital technologies, offers a timely and innovative solution.
Smart farming, also known as intelligent agriculture, represents a modern stage in the development of agricultural science and practice. Its defining feature lies in the active application of artificial intelligence methods, particularly machine learning and deep learning, to address specific tasks aimed at ensuring sustainable crop production. (Research purpose) The aim of this study is to analyze data structures and compare machine learning and deep learning algorithms used in used in crop yield prediction. (Materials and methods) Using a convergent approach and applying methods of cognitive and semantic analysis, the authors examined the subject area of artificial intelligence applications in crop yield prediction. The study also explores key aspects related to the structure of input data, the main stages of implementing predictive models, and the most widely used machine learning and deep learning methods. (Results and discussion) The study presents the core data structure and methods for data acquisition, along with a typical workflow for implementing predictive analytics models for crop yield prediction. The most commonly used machine learning and deep learning methods are identified and their functional characteristics are examined in detail. Comparative analysis demonstrates that deep learning and hybrid approaches outperform traditional machine learning methods in terms of prediction accuracy, as measured by standard error metrics. (Conclusions) The findings confirm the advantages of deep learning methods (mean R² = 0.85) and hybrid approaches (mean R² = 0.87) in crop yield prediction under varying conditions and management interventions. Future research may focus on adapting modern AI approaches to spatial land use objects and crop types, with an emphasis on remote sensing data.
Accurate, timely, and non-invasive diagnosis of plant diseases is essential in the industrial cultivation of strawberries, as it helps minimize yield losses and reduce treatment costs. With the advancement of unmanned aerial vehicles and sensor technologies, remote sensing has emerged as a promising tool for monitoring crop health and detecting diseases. Early detection is especially important for sensitive crops such as garden strawberries. (Research purpose) The research aims to evaluate the potential of using multispectral sensors and unmanned aerial vehicles for detecting fungal diseases in garden strawberries under field conditions. (Materials and methods) Aerial imaging of strawberry plants affected by white leaf spot was carried out at the experimental nursery of the Siberian Federal Research Center for Agro-BioTechnologies of the RAS (SibFRC ABT RAS). A DJI Phantom 4 Multispectral quadcopter equipped with a multispectral camera was used for data collection. The acquired imagery underwent preliminary processing, including orthophotomap generation and extraction of spectral and textural features from the images. (Results and discussion) Analysis of the multispectral data enabled the identification of informative feature sets for distinguishing between healthy and fungus-infected strawberry plants. A disease detection model developed using the Random Forest algorithm, achieved a classification accuracy of 77%. (Conclusions) To improve classification accuracy, further research involving sensors with higher spatial resolution is recommended. Another promising direction is the development of classification models based on convolutional neural networks, which offer improved performance through deeper image analysis. The results confirm the potential of UAV-based multispectral imaging for effective crop disease monitoring.
INNOVATIVE TECHNOLOGIES AND EQUIPMENT
The development of new wear-resistant hard-alloy compositions for hardfacing the working surfaces of components operating in highly abrasive environments, particularly soil, is one of the most effective strategies for mitigating abrasive wear and its effects. Industrially produced iron–carbon-based hard alloys have relatively low abrasive wear resistance. (Research purpose) To develop new hard alloys based on high-alloy cast irons that increase wear resistance and improve the efficiency of hardfacing coatings applied to wear-prone components of tillage machinery. (Materials and methods) A priori analysis indicates that increasing boron content generally enhances the abrasion resistance of steels and hard alloys. However, the specific effects of boron alloying, particularly in iron–carbon-based hard alloys, remain complex and insufficiently studied. Based on previous research, the recommended boron content in such alloys ranges from 0.5 to 6.0 percent. This study also explores the combined effect of boron alloying with manganese and nickel. The research methodology included comparative laboratory and operational field life testing of specimens and full-scale components coated with various types of hard-alloy overlays. (Results and discussion) Four newly developed boron-containing hard alloys were evaluated through comparative laboratory and field tests. Among them, the alloy designated PR-FB3Kh showed the highest performance, demonstrating up to 1.6 times higher relative wear resistance when applied by hardfacing, compared to the leading industrially produced alloy PG-FBKh-6-2. In certain applications, these new alloys may serve as cost-effective alternatives to industrially produced hard-alloy compositions containing expensive cast tungsten carbide additives. (Conclusions) As a result of the research and testing, two new alloys PR-FB3Kh and PR-FB2.5Kh were developed. These alloys are distinguished primarily by their elevated boron content (up to 3.2 percent) and high wear resistance. They present a high-quality, cost-effective alternative to conventional iron-carbon-based alloys that incorporate cast tungsten carbide (WC).
Recent advancements in robotics and automation have significantly contributed to the progress of precision agriculture. This study presents the development of an automated machine-tractor unit (MTU) designed for grass mowing, incorporating universal mechatronic control modules. (Research purpose) The purpose of this research is to design a functional and technological scheme for an automated machine-tractor unit and to develop universal mechatronic modules that can be mounted onto the mechanical control elements typically operated by a human driver. These modules are intended to enable the automated execution of the grass mowing process. (Materials and methods) A functional and technological scheme of the machine-tractor unit was developed. The unit consists of a remote control system, a tractor, an access control and management system (ACMS), and a technological implement. The methodology for the automatic control of the machine-tractor unit in an agro-landscape was described. A theoretical justification was provided for the design and technological parameters of the universal mechatronic modules used to control the clutch and braking systems. Calculations were conducted for the mechatronic module mechanism, including the determination of the screw drive gear ratio, screw travel, and nut displacement speed. A functional relationship was established between the pedal stroke velocity (change in pedal angle) and the nut displacement speed in the mechatronic actuation module. Control software for the universal mechatronic modules was developed using a programming language suitable for the selected controller. (Results and discussion) Automatic control of the machine-tractor unit was successfully implemented in an agro-landscape setting using a remote control panel, an LTZ-120B wheeled tractor, and a KRN-2.4 rotary mower. Field tests were conducted to evaluate the interaction between the control software and the hardware components of the universal mechatronic control modules. Comparative experimental studies were performed during straight-line mowing operations to evaluate the system performance under both manual control (with an operator) and automated control (using mechatronic actuators). (Conclusions) Preliminary tests of the automated agricultural machine-tractor unit demonstrated that its operational performance indicators remained within acceptable limits during mower-assisted operations. Specifically, the system achieved a productivity rate of 3.56 hectares per hour of effective operation, maintained a working speed of 10 ± 0.3 kilometers per hour, and ensured a grass cutting height of 8 ± 1 centimeters.
The paper highlights the importance of improving arable land productivity. The production of a balanced forage mass is influenced by crop selection, sowing methods, and seed placement precision. (Research purpose) The study aims to identify key factors and assess their impact on the structural parameters and operating modes of the seeding mechanism. (Materials and methods) Mosaic sowing was performed using an SN-16 seeder equipped with a modified hopper. The experimental design considered belt speed, crop type, and hopper shape as significant factors. Response variables included deviations from the target sowing coordinates and the performance indicators of the seeding mechanism. A full factorial experimental design matrix was developed to evaluate the effects of these factors. (Results and discussion) A series of trials was conducted using a laboratory setup, followed by planned field testing of the SN-16 seeder equipped with the modified hopper. Sowing quality was evaluated based on seed placement depth, deviation from the centerline, and plant density per unit area. These indicators varied across different sections of the test field, but overall, the sowing quality met the established agronomic standards. For grain crops, the deviation of the average seeding depth from the target value did not exceed 15 percent, while for small-seeded crops, it remained within 5 percent in most cases. Depth variation was primarily attributed to uneven terrain across the test plots. Field germination, defined as the proportion of emerged plants to the number of seeds sown, reached 90 percent. (Conclusions) The use of the SN-16 seeder equipped with a modified hopper for mosaic sowing demonstrates promising potential. The cultivation quality of the tested crops was found to be satisfactory according to key agronomic indicators.
The paper highlights that preserving and enhancing the soil fertility of agricultural lands remains one of the most pressing challenges for the national economy. In soil conservation farming systems, no-till soil cultivation plays a crucial role in preventing wind and water erosion, regulating the soil’s physical, chemical, and biological properties, and optimizing the use of soil and climatic resources to ensure higher and more stable crop yields. (Research purpose) To develop an automated layer-by-layer soil tillage machine that utilizes a highly turbulent air jet to improve soil fertility and reduce the traction resistance of the machine-tractor unit. (Materials and methods) A design was developed for an automated layer-by-layer soil tillage machine utilizing a highly turbulent air jet. Upon receiving a signal from the control system, pneumatic solenoid valves are activated supplying compressed air to the working tools. The machine is equipped with needle rollers having needles up to 10 centimeters long and disc mills capable of reaching tillage depths of 15–20 centimeters for root crops and 8–12 centimeters for grain crops. The working tools include two arc-shaped blades arranged in sequence with a spacing of 15–20 centimeters; the front blade operates at a depth of 10–12 centimeters, while the rear blade is positioned 10–12 centimeters lower to enable multi-layer soil tillage. (Results and discussion) The results demonstrate that the proposed design delivers impulse bursts of compressed air that loosens the soil without disturbing its structure. This improves operational efficiency and supports both continuous and row-specific tillage. Moreover, the system enhances quality indicators and reduces fuel consumption. (Conclusions) The development of an automated layer-by-layer soil tillage machine utilizing a highly turbulent air jet offers a promising solution for preserving and improving soil fertility.
The paper demonstrates that preventing the degradation of mountain meadows and pastures, mitigating the decline in the productivity of mountain grass lands, and supporting their restoration require the application of mineral fertilizers. It also highlights the lack of small-sized machinery suitable for treating mountainous areas.(Research purpose) The aim of this research is to develop a small-sized laboratory prototype of a unit for applying mineral fertilizers on sloped mountainous terrain covered with natural grass stands on fallow forage lands.(Materials and methods) The proposed technology was substantiated, and a laboratory prototype of the unit was created. Technical evaluations and field tests of both the unit and the technology were conducted in the mountainous region of the Republic of North Ossetia–Alania (Dargavs Basin). Additionally, a technical specification was compiled to support the development of the prototype.(Results and discussion) The research focused on the technology for applying granular fertilizers both to the surface and into slits across mountain slopes, as well as on determining the optimal application rates and methods when using a small-sized. As a result, a unit design incorporating pendulum-type sowing mechanisms was developed, and a small-sized laboratory prototype for surface application of mineral fertilizers was produced. The functional performance indicators of the unit were established. The laboratory prototype was confirmed to meet agrotechnical requirements and comply with the technical specification. Furthermore, it was found that using the unit increases labor productivity and enhances the productivity of mountain forage lands by 15–20 percents. (Conclusions) The use of a small-sized unit contributes to reducing degradation processes on sloped plots by accelerating the restoration of both the quality and quantity of perennial grasses on fallow forage lands. The yield of green biomass increased across various altitudinal zones and slope exposures as follows: by 20.58 tonnes per hectare in the meadow-steppe zone, by 9.53 tonnes per hectare in the subalpine zone, and by 5.73 tonnes per hectare in the alpine zone. The feasibility of further improving and applying the prototype on small-contour mountainous fallow areas with slopes of up to 13 degrees has been confirmed.